THine Value SerDes Starter Kit for Embedded Cameras Significantly Reduces Cable Extension Design Time for MIPI Cameras
2022.10.25
- Article
- Column
Many industrial devices incorporate camera functions. Typical examples include inspection/measurement equipment for factory production lines, security cameras, medical equipment, and material handling systems. A more familiar example is equipping vending machines with a camera function.
One of the most vexing problems for engineers developing industrial equipment incorporating such camera functions is the selection and operation of a camera interface. Many industrial devices are relatively large, and there are cases where the transmission distance of video data output from a camera module needs to be extended. On the other hand, MIPI CSI-2, a camera interface that is becoming widely used in the field of embedded camera systems, has the advantages of high-speed support and low power consumption; however, it has a transmission distance of only 30 cm at most. This imposes the need to extend the transmission distance somehow.
What kind of methods are there? One approach is to use SerDes (combining "Serializer" and "Deserializer"), which supports long-distance transmission. Specifically, the cable can be extended by placing a transmitter IC on the camera module side and a receiver IC on the system side that captures images acquired by the camera, which are the start and end points of the transmission line to be extended (Figure 1).
However, this poses a problem. The issue is ensuring that the camera system operates with sufficient transmission distance in the early design phase. Once the hardware, software, design, and prototyping are in place and performance is finally verified, the system must be redesigned if it is found not to work correctly or if the design transmission distance is insufficient. This can waste a lot of time and money.
One of the most vexing problems for engineers developing industrial equipment incorporating such camera functions is the selection and operation of a camera interface. Many industrial devices are relatively large, and there are cases where the transmission distance of video data output from a camera module needs to be extended. On the other hand, MIPI CSI-2, a camera interface that is becoming widely used in the field of embedded camera systems, has the advantages of high-speed support and low power consumption; however, it has a transmission distance of only 30 cm at most. This imposes the need to extend the transmission distance somehow.
What kind of methods are there? One approach is to use SerDes (combining "Serializer" and "Deserializer"), which supports long-distance transmission. Specifically, the cable can be extended by placing a transmitter IC on the camera module side and a receiver IC on the system side that captures images acquired by the camera, which are the start and end points of the transmission line to be extended (Figure 1).

Figure 1. Cable extension via long-distance transmission-capable interface
However, this poses a problem. The issue is ensuring that the camera system operates with sufficient transmission distance in the early design phase. Once the hardware, software, design, and prototyping are in place and performance is finally verified, the system must be redesigned if it is found not to work correctly or if the design transmission distance is insufficient. This can waste a lot of time and money.
No Evaluation Kit Optimized for Early Design Stage Evaluation
To avoid such a situation, confirming the operation and evaluating transmission capacity in advance at the early design phase is preferable. In other words, by combining a camera module equipped with the image sensor, a transmitter IC/receiver IC, and cables and transmitting the video signals, one can confirm whether the equipment works without problems and if the video can be transmitted over the required distance.
All semiconductor manufacturers with SerDes devices in their lineup offer evaluation boards to support such preliminary evaluations. For example, THine Electronics offers an evaluation board with the THCV241A transmitter IC and the THCV242A receiver IC, respectively.
However, these evaluation boards do not provide a straightforward process for utilization in the design stage. It takes much work with the hardware and software before the evaluation process can begin.
All semiconductor manufacturers with SerDes devices in their lineup offer evaluation boards to support such preliminary evaluations. For example, THine Electronics offers an evaluation board with the THCV241A transmitter IC and the THCV242A receiver IC, respectively.
However, these evaluation boards do not provide a straightforward process for utilization in the design stage. It takes much work with the hardware and software before the evaluation process can begin.
Hardware and Software Development is Required from the Pre-evaluation Stage
What exactly is the hassle involved?
First, the current evaluation boards are highly versatile in terms of hardware, with board specifications that are not oriented toward any specific market or application. For example, MIPI CSI-2 input/output connectors use pin headers, which have the advantage of easy fabrication. Still, there are generally no camera modules or image acquisition platforms that can connect without fabrication. In addition, the input/output connector for the V-by-One HS, which is the long-distance transmission part, uses a highly versatile SMA connector, which is convenient for users to create and connect a board that converts to any connector they wish. On the flip side, cables that connect to SMA connectors and support long-distance transmission are rare. Therefore, hardware fabrication cannot be avoided even if a user tries to connect a particular device or cable for preliminary evaluation.
Next, from a software perspective, the camera module, SerDes, and image capture platform all require configuration and environment setting to operate. Taking transmitter IC/receiver IC as an example, it is necessary to write register codes according to the data transmission speed of video signals and the transmission path configuration of video signals/control signals. Typically, a preliminary evaluation is conducted to reduce rework after design, but many resources being allocated for such an initial evaluation may be a case of misaligned priorities.
First, the current evaluation boards are highly versatile in terms of hardware, with board specifications that are not oriented toward any specific market or application. For example, MIPI CSI-2 input/output connectors use pin headers, which have the advantage of easy fabrication. Still, there are generally no camera modules or image acquisition platforms that can connect without fabrication. In addition, the input/output connector for the V-by-One HS, which is the long-distance transmission part, uses a highly versatile SMA connector, which is convenient for users to create and connect a board that converts to any connector they wish. On the flip side, cables that connect to SMA connectors and support long-distance transmission are rare. Therefore, hardware fabrication cannot be avoided even if a user tries to connect a particular device or cable for preliminary evaluation.
Next, from a software perspective, the camera module, SerDes, and image capture platform all require configuration and environment setting to operate. Taking transmitter IC/receiver IC as an example, it is necessary to write register codes according to the data transmission speed of video signals and the transmission path configuration of video signals/control signals. Typically, a preliminary evaluation is conducted to reduce rework after design, but many resources being allocated for such an initial evaluation may be a case of misaligned priorities.
Good to Go Once an Image Appears
To this end, we have prepared the MIPI Camera Serdes Starter Kit, which focuses on reducing the time and cost burden of SerDes application in embedded cameras for industrial equipment. The hardware configuration consists of a transmitter board with the THCV241A transmitter IC, which supports V-by-One HS, a receiver board with the THCV242A receiver IC, and an Ethernet cable using the RJ-45 connector. The transmitter board is connected to the corresponding camera module and the receiver board to the specified grabber board (image capturing device), and the transmitter board and receiver board are connected by an Ethernet cable (Figure 2). With this kit, you can start evaluating SerDes from the beginning without spending time on hardware development, software development, and environment creation.
Now, let us explain how we have eliminated the need to develop hardware and software, in addition to not needing to create an environment before a picture is generated.
First, on hardware, we specified commercially available camera modules and image capture environments that are compatible with the system and pre-matched the connectors of the transmitter and receiver boards to be connected. Next, regarding software, we have secured the complete set of software necessary for its operation (*Provided by THine or a third party), eliminating the need for users to prepare their software. There are four compatible camera modules, one being Shikino High Tech's 1.3 MP product and a lineup of cameras from the German FRAMOS, including their 2 MP, 5 MP, and 8 MP products. Various companies offer these products as embedded camera modules for industrial equipment. For the grabber board as the image acquisition environment, we specified a product by DOTHINKEY from China. DOTHINKEY's grabber boards are widely used in the Chinese market and are known for their high cost-performance ratio. (*Grabber boards and camera modules must be ordered separately from this kit).
Furthermore, the connection connector for the long-distance transmission cable to be placed on both the transmitter and receiver boards uses the RJ-45 standard, which is widely used in the industrial equipment field. Ethernet cables adopting RJ-45 are readily available, and it is easy to obtain cables of multiple transmission quality grades, such as CAT6 and CAT7, from a single source. In addition to an expansive lineup of cable lengths, the fact that one could relatively easily create their cable at a desired length is also a high point in transmission evaluation. The kit will also include a cable for operation verification.
The kit allows the user to pre-evaluate SerDes from a picture-ready state, allowing them to replace the Ethernet cable to confirm transmission capacity and proceed with initial cable review. Highly effective evaluation results can be obtained, mainly when users apply RJ-45 connectors and Ethernet cables in their mass production designs.
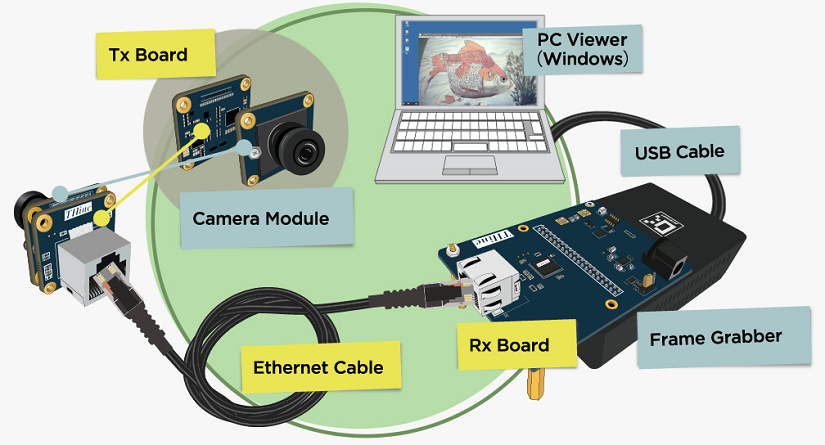
Figure 2. System configuration of the SerDes Starter Kit for Embedded Cameras
Now, let us explain how we have eliminated the need to develop hardware and software, in addition to not needing to create an environment before a picture is generated.
First, on hardware, we specified commercially available camera modules and image capture environments that are compatible with the system and pre-matched the connectors of the transmitter and receiver boards to be connected. Next, regarding software, we have secured the complete set of software necessary for its operation (*Provided by THine or a third party), eliminating the need for users to prepare their software. There are four compatible camera modules, one being Shikino High Tech's 1.3 MP product and a lineup of cameras from the German FRAMOS, including their 2 MP, 5 MP, and 8 MP products. Various companies offer these products as embedded camera modules for industrial equipment. For the grabber board as the image acquisition environment, we specified a product by DOTHINKEY from China. DOTHINKEY's grabber boards are widely used in the Chinese market and are known for their high cost-performance ratio. (*Grabber boards and camera modules must be ordered separately from this kit).
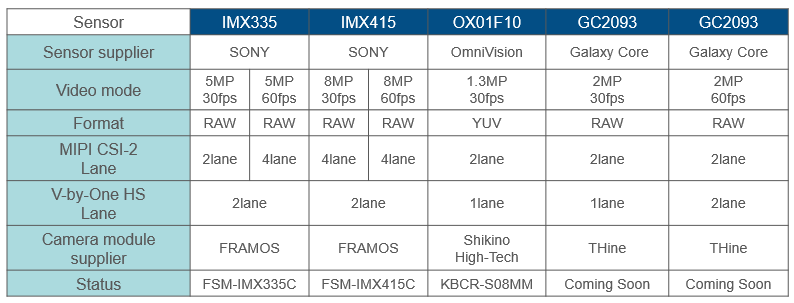
Figure 3. Compatible camera module lineup
Furthermore, the connection connector for the long-distance transmission cable to be placed on both the transmitter and receiver boards uses the RJ-45 standard, which is widely used in the industrial equipment field. Ethernet cables adopting RJ-45 are readily available, and it is easy to obtain cables of multiple transmission quality grades, such as CAT6 and CAT7, from a single source. In addition to an expansive lineup of cable lengths, the fact that one could relatively easily create their cable at a desired length is also a high point in transmission evaluation. The kit will also include a cable for operation verification.
The kit allows the user to pre-evaluate SerDes from a picture-ready state, allowing them to replace the Ethernet cable to confirm transmission capacity and proceed with initial cable review. Highly effective evaluation results can be obtained, mainly when users apply RJ-45 connectors and Ethernet cables in their mass production designs.
Starter Kit as a Reference Design
Once feasibility is confirmed in the SerDes pre-evaluation, the user would move on to design work based on their projects. This is the transition to so-called mass production design. This kit will also play an active role in this design work.
THine provides the user with a schematic and BOM (bill of materials) for each of the transmitter/receiver boards included in the kit and register codes for THCV241A and THCV242A. In this way, the hardware/software environment in a picture-ready state can function as a "picture-ready solution" together with these data as a reference design for mass production design. Users can check the "solution" against arbitrary designs for easy verification and debugging.
THine provides the user with a schematic and BOM (bill of materials) for each of the transmitter/receiver boards included in the kit and register codes for THCV241A and THCV242A. In this way, the hardware/software environment in a picture-ready state can function as a "picture-ready solution" together with these data as a reference design for mass production design. Users can check the "solution" against arbitrary designs for easy verification and debugging.
GUI Register Generation Tool to Support Transition to Mass Production Design
In addition to the THCV241A and THCV242A reference register codes in this kit configuration, a dedicated Graphical User Interface (GUI) tool that enables the automatic generation of register codes will be available simultaneously (Figure 4). This GUI tool allows the automatic generation of reference register codes for any camera module or peripheral configuration the user selects. Previously, users had to write code from scratch by reading datasheets, applications, and register maps. Now, this GUI tool can significantly reduce the workload.
Figure 5 summarizes the process described so far. The starter kit challenges users to lower their barriers by breaking down the SerDes adoption process step-by-step.

Figure 4. GUI register generation tool
Figure 5 summarizes the process described so far. The starter kit challenges users to lower their barriers by breaking down the SerDes adoption process step-by-step.
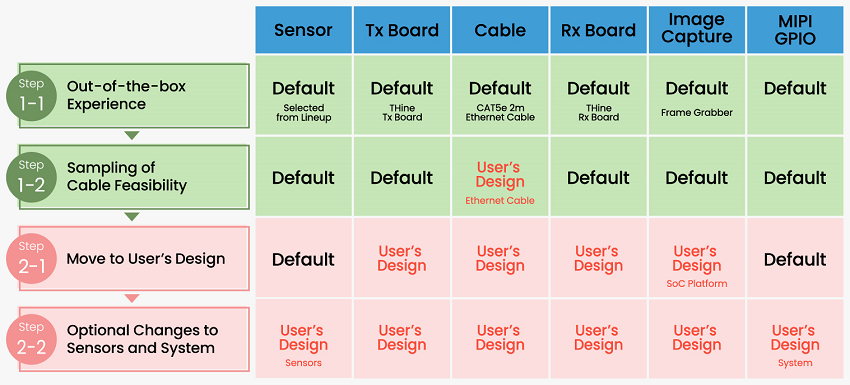
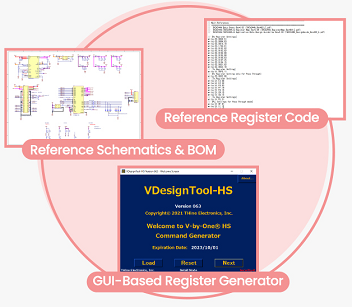
Figure 5. SerDes development process provided by the starter kit
Future Lineup in Place to Meet Various Camera Needs
To ensure normal operation in the default state, the starter kit is pre-configured for compatible camera modules, cables (connectors and harnesses), and grabber boards. There is no denying that this results in a limited lineup and needs that can be addressed. After the first starter kit's release, we plan to gradually expand our lineup of options while listening to user feedback.
End
End
Related Contents
- What is the High-speed Interface Standard MIPI? Going Beyond the Boundaries of Mobile Devices to Automotive Applications
- In-depth Comparison of Camera Modules for Industrial Equipment: Pros and Cons of UVC Cameras, IP Cameras, Wi-Fi Cameras, and MIPI Cameras
- MIPI Camera SerDes Starter Kit for an Embedded Camera System in Long Reach
- Extending MIPI Transmission with V-by-One HS: Simplifying SerDes Chipset Selection for Embedded Cameras (Sub-Link Part)
- Extending MIPI Transmission with V-by-One HS: Simplifying SerDes Chipset Selection for Embedded Cameras (Main-Link Part)