THine Value A Simple Solution to I/O Issues without FGPAs: Serial Transceivers that Bundle and Send GPIO and I2C Signals Now Available!
2023.07.20
- Article
- Column
Currently, the number of camera modules and various sensors installed in electronic equipment such as factory automation, office, security/surveillance, and transportation equipment in the industrial equipment market is increasing. The reasons behind this are lower prices for camera modules, improved usability, and increased efforts to address the Internet of Things (IoT). Of course, many camera modules and various sensors can dramatically improve the functionality and performance of these electronic devices, as well as greatly enhance their usability. The benefits gained are monumental.
On the other hand, however, using these camera modules and various sensors adds to the problem of increased design difficulty. Examples of these difficulties include: 1. The production line is too long to send video data transmission when trying to monitor the entire production line with cameras. 2. Too many cables sending the data acquired by the various sensors increase the weight of the main body of the electronic device. 3. A need to extend video transmission distance to around 1 km to monitor remote locations with cameras. 4. A need to make the high-speed transmission path connecting the sensors dustproof and to make the sensors easy to attach and detach due to a subpar installation environment from industrial equipment. While solving these problems, camera modules and various sensors are used as needed to improve the functionality, performance, and usability of electronic equipment. This is the challenge that industrial equipment developers are currently facing.
On the other hand, however, using these camera modules and various sensors adds to the problem of increased design difficulty. Examples of these difficulties include: 1. The production line is too long to send video data transmission when trying to monitor the entire production line with cameras. 2. Too many cables sending the data acquired by the various sensors increase the weight of the main body of the electronic device. 3. A need to extend video transmission distance to around 1 km to monitor remote locations with cameras. 4. A need to make the high-speed transmission path connecting the sensors dustproof and to make the sensors easy to attach and detach due to a subpar installation environment from industrial equipment. While solving these problems, camera modules and various sensors are used as needed to improve the functionality, performance, and usability of electronic equipment. This is the challenge that industrial equipment developers are currently facing.
Replacing Parallel Transmissions with Serial Transmissions
Intending to solve these problems, THine Electronics has launched a new serial transceiver IC, THCS253/THCS254. Our code name for this new product is IOHA:B (pronounced I/O Hub).
The new product integrates a transmitter (transmitter circuit and serializer) and receiver (receiver circuit and deserializer) on a single chip. For this reason, it is also called a SerDes transceiver IC. Two new products are used during application, one as the primary chip and the other as the secondary chip. The two chips are connected with two pairs of differential lines, one uplink and the other downlink. In other words, a full-duplex transmission system that simultaneously transmits and receives signals can be realized by providing separate uplink and downlink signal lines. It is envisioned to replace parallel transmission consisting of many signal lines with serial transmission using only two pairs of differential lines (Fig. 1).
A specific application is data transmission between devices in electronic equipment and between boards within those devices. The more than 30 signal lines connecting devices and boards can be bundled into just two pairs of differential lines (four signal lines), thus reducing the number of wiring cables and the total weight and extending the transmission distance. In other words, this can solve all of the issues mentioned at the beginning of this article.
THine Electronics had already commercialized a previous serial transceiver IC, the THCS251/THCS252, at the end of 2019, which can be used almost the same way. The new THCS253/THCS254 models introduced to the market now are the successor versions of these previous products. The latest products inherit the essential functions of the earlier version while making significant new changes. These changes include the addition of one or two I2C and multiple general-purpose IOs (GPIOs) as bundled signal lines. The THCS253 provides up to 32 GPIOs, and the TCHS254 offers up to 20. In addition, both models have one I2C system equipped by default. If the user performs the prescribed settings, two GPIOs can be assigned to I2C. This means up to two I2C systems can be bundled with GPIOs for serial transmission.
The new product integrates a transmitter (transmitter circuit and serializer) and receiver (receiver circuit and deserializer) on a single chip. For this reason, it is also called a SerDes transceiver IC. Two new products are used during application, one as the primary chip and the other as the secondary chip. The two chips are connected with two pairs of differential lines, one uplink and the other downlink. In other words, a full-duplex transmission system that simultaneously transmits and receives signals can be realized by providing separate uplink and downlink signal lines. It is envisioned to replace parallel transmission consisting of many signal lines with serial transmission using only two pairs of differential lines (Fig. 1).
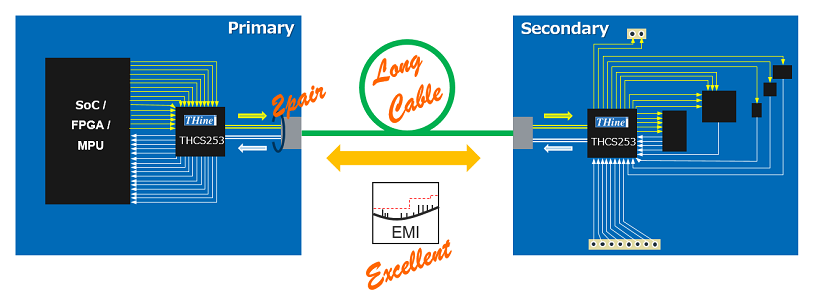
Fig. 1 Replacing parallel transmissions with serial transmissions
A specific application is data transmission between devices in electronic equipment and between boards within those devices. The more than 30 signal lines connecting devices and boards can be bundled into just two pairs of differential lines (four signal lines), thus reducing the number of wiring cables and the total weight and extending the transmission distance. In other words, this can solve all of the issues mentioned at the beginning of this article.
THine Electronics had already commercialized a previous serial transceiver IC, the THCS251/THCS252, at the end of 2019, which can be used almost the same way. The new THCS253/THCS254 models introduced to the market now are the successor versions of these previous products. The latest products inherit the essential functions of the earlier version while making significant new changes. These changes include the addition of one or two I2C and multiple general-purpose IOs (GPIOs) as bundled signal lines. The THCS253 provides up to 32 GPIOs, and the TCHS254 offers up to 20. In addition, both models have one I2C system equipped by default. If the user performs the prescribed settings, two GPIOs can be assigned to I2C. This means up to two I2C systems can be bundled with GPIOs for serial transmission.
Easy Support for Optical/Wireless
Our new products provide users with further advantages while maintaining the advantages of the existing THCS251/THCS252 models. First, let us review the benefits inherited from the conventional products. There are six major advantages.
The first is that parallel transmission can be replaced by serial transmission, thus reducing the number of wiring cables. For example, with the new THCS253, 34 signal lines (32 GPIO + 1 I2C) can be reduced to just 2 differential pairs (4 lines). This means that the number of wiring cables can be reduced by up to 88%. As a result, this allows the same throughput of 34 cables to pass through narrow spaces that may not have accommodated this number of cables. For example, this contributes to the compactness of electronic devices such as inkjet printers.
The second advantage is the reduction in the total weight of the wiring cable. This is due to the reduced number of wiring cables, which has a significant effect. For example, this type of weight reduction may reduce the weight of a drone, allowing for longer battery run time and, thus, longer flight times.
The third advantage is the simplified process of connecting wiring cables. This is due to the reduced number of cables that need to be connected. As a result, wiring errors can be diminished, and work efficiency can be improved.
The fourth advantage is extending transmission distance while maintaining signal quality (signal integrity). In parallel transmission, the available transmission distance is at most 1 m when the clock frequency is 100 MHz. On the other hand, for serial transmission, a continuous time linear equalizer (CTLE), which compensates for the frequency characteristics of the sent signal and shapes the waveform, is installed in the receiver circuit so the transmission distance can be extended to approximately 10 m at a clock frequency of 100 MHz (transmission speed of 3.0 Gbps), albeit dependent on the quality of the wiring cable used.
The fifth advantage is reducing the radiation level of electromagnetic interference (EMI). There are two reasons this is the case. The first is the use of a clock signal-embedded SerDes circuit. The other reason is that the transmission medium is a differential cable with two signal lines. Noise radiated from each signal line cancels out.
The sixth advantage is the ability to standardize design. The conventional THCS251 provides a maximum of 35 GPIOs, but there are few use cases where all these must be used. This generates excess terminals (vacant terminals), which can be effectively used to standardize the design. For example, the extra terminals can connect between the microcontroller/FPGA and the connector in advance. In this way, even if the functions of multiple models differ slightly, the hardware design of signal transmission paths, etc., remains the same, and differences in functions can be absorbed by simply assigning new signals to the extra terminals. Moreover, the conventional THCS251/THCS252 models have a function that allows the ratio of general-purpose inputs (GPI) to general-purpose outputs (GPO) to be set in four steps. This can increase the scope for absorbing differences in functionality. In other words, these models made it possible to share the same design to realize multiple models with only one hardware design.
In addition to these advantages, another major feature is the ease of conversion to optical and wireless. The new product uses a full-duplex transmission system with downlink and uplink transmission paths, respectively. Therefore, connecting an optoelectronic conversion device or a short-distance wireless communication device (millimeter wave communication device) to each can make the connection between devices or boards optical or wireless. This, as a result, dramatically expands the range of applications. Making the system optical allows it to be applied to applications where the distance between two electronic devices is far apart (several tens to several hundreds of meters), where the noise environment is poor, or where electrical isolation is required (Fig. 2).
On the other hand, wireless technology allows for use in factories and other applications requiring dustproofing and electrical insulation (Fig. 3).
The first is that parallel transmission can be replaced by serial transmission, thus reducing the number of wiring cables. For example, with the new THCS253, 34 signal lines (32 GPIO + 1 I2C) can be reduced to just 2 differential pairs (4 lines). This means that the number of wiring cables can be reduced by up to 88%. As a result, this allows the same throughput of 34 cables to pass through narrow spaces that may not have accommodated this number of cables. For example, this contributes to the compactness of electronic devices such as inkjet printers.
The second advantage is the reduction in the total weight of the wiring cable. This is due to the reduced number of wiring cables, which has a significant effect. For example, this type of weight reduction may reduce the weight of a drone, allowing for longer battery run time and, thus, longer flight times.
The third advantage is the simplified process of connecting wiring cables. This is due to the reduced number of cables that need to be connected. As a result, wiring errors can be diminished, and work efficiency can be improved.
The fourth advantage is extending transmission distance while maintaining signal quality (signal integrity). In parallel transmission, the available transmission distance is at most 1 m when the clock frequency is 100 MHz. On the other hand, for serial transmission, a continuous time linear equalizer (CTLE), which compensates for the frequency characteristics of the sent signal and shapes the waveform, is installed in the receiver circuit so the transmission distance can be extended to approximately 10 m at a clock frequency of 100 MHz (transmission speed of 3.0 Gbps), albeit dependent on the quality of the wiring cable used.
The fifth advantage is reducing the radiation level of electromagnetic interference (EMI). There are two reasons this is the case. The first is the use of a clock signal-embedded SerDes circuit. The other reason is that the transmission medium is a differential cable with two signal lines. Noise radiated from each signal line cancels out.
The sixth advantage is the ability to standardize design. The conventional THCS251 provides a maximum of 35 GPIOs, but there are few use cases where all these must be used. This generates excess terminals (vacant terminals), which can be effectively used to standardize the design. For example, the extra terminals can connect between the microcontroller/FPGA and the connector in advance. In this way, even if the functions of multiple models differ slightly, the hardware design of signal transmission paths, etc., remains the same, and differences in functions can be absorbed by simply assigning new signals to the extra terminals. Moreover, the conventional THCS251/THCS252 models have a function that allows the ratio of general-purpose inputs (GPI) to general-purpose outputs (GPO) to be set in four steps. This can increase the scope for absorbing differences in functionality. In other words, these models made it possible to share the same design to realize multiple models with only one hardware design.
In addition to these advantages, another major feature is the ease of conversion to optical and wireless. The new product uses a full-duplex transmission system with downlink and uplink transmission paths, respectively. Therefore, connecting an optoelectronic conversion device or a short-distance wireless communication device (millimeter wave communication device) to each can make the connection between devices or boards optical or wireless. This, as a result, dramatically expands the range of applications. Making the system optical allows it to be applied to applications where the distance between two electronic devices is far apart (several tens to several hundreds of meters), where the noise environment is poor, or where electrical isolation is required (Fig. 2).
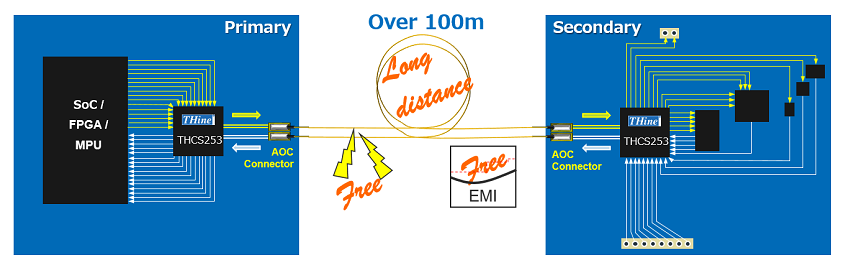
Fig. 2 Facilitates conversion to optical
On the other hand, wireless technology allows for use in factories and other applications requiring dustproofing and electrical insulation (Fig. 3).
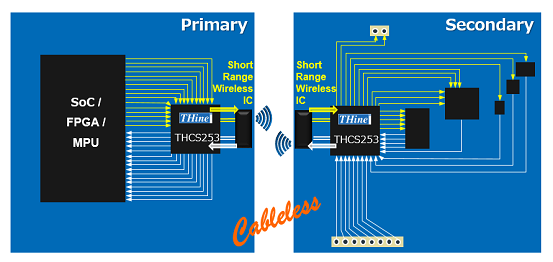
Fig. 3 Facilitates conversion to wireless
No Hardware Redesign Required for Sudden Addition of New Functions
Thus, THine Electronics' serial transceiver ICs offer the multiple advantages described above, even in conventional products. In addition, the new THCS253/THCS254 models have the advantage of I2C compatibility, significantly increasing the design freedom of the input/output interface (I/O) section.
In general, it is not uncommon for the development of electronic equipment to undergo sudden changes in design after design work has begun. The addition of new features, for example. In this case, depending on the functions to be added, the number of signal lines to be exchanged with sub-boards, etc., may increase, forcing changes in hardware design, such as signal transmission paths. Of course, the need for a redesign means an increase in person-hours, project delivery time, and cost.
If possible, hardware redesigns should be avoided even in the event of sudden design changes. Our new products are very effective in these kind of scenarios. With our support for I2C, each pin can be freely customized by accessing the internal registers and rewriting data through this compatibility. In other words, the hardware design, such as signal transmission paths, can be left unchanged while responding extremely flexibly to additional functions by simply rewriting internal registers (Fig. 4).
As mentioned above, the existing THCS251/THCS252 models also have a function that allows the number ratio of GPI and GPO to be set in four steps, which can be used to accommodate sudden design changes to some extent. However, the scope for customization is far more significant in our new models. Therefore, using our new models can significantly reduce the probability of redesigning hardware during design change compared to the previous models.
One might ask, "Was there no effective remedy that could prevent the need for hardware redesign?" Of course, this could be achieved using FPGAs. However, this brought a significant disadvantage ?increased design labor involved in designing the circuity inside the FPGA and the layout design of the printed circuit board. In addition, costs would increase. It would be difficult to decide to install FPGAs in the I/O section in advance simply due to the possibility of future change, such as the addition of functions, after starting the design in the first place.
However, the new models integrate the circuity for customization via I2C on a single chip, so unlike FPGAs, almost no additional design effort is required at the time of introduction. When other functions are added, they can be handled simply by rewriting the built-in registers, eliminating the need for any hardware redesign, such as signal transmission paths.
In Part 1 of this article, we described the changes made to the new THCS253/THCS254 models from the previous products, namely, I2C support in addition to GPIO, and introduce the advantages of this change, which is that the I/O section can be customized with a high degree of freedom (Fig. 5).
In Part 2, in addition to explaining this change in more detail, another change, the introduction of synchronous/asynchronous mode, will be described.
End
In general, it is not uncommon for the development of electronic equipment to undergo sudden changes in design after design work has begun. The addition of new features, for example. In this case, depending on the functions to be added, the number of signal lines to be exchanged with sub-boards, etc., may increase, forcing changes in hardware design, such as signal transmission paths. Of course, the need for a redesign means an increase in person-hours, project delivery time, and cost.
If possible, hardware redesigns should be avoided even in the event of sudden design changes. Our new products are very effective in these kind of scenarios. With our support for I2C, each pin can be freely customized by accessing the internal registers and rewriting data through this compatibility. In other words, the hardware design, such as signal transmission paths, can be left unchanged while responding extremely flexibly to additional functions by simply rewriting internal registers (Fig. 4).
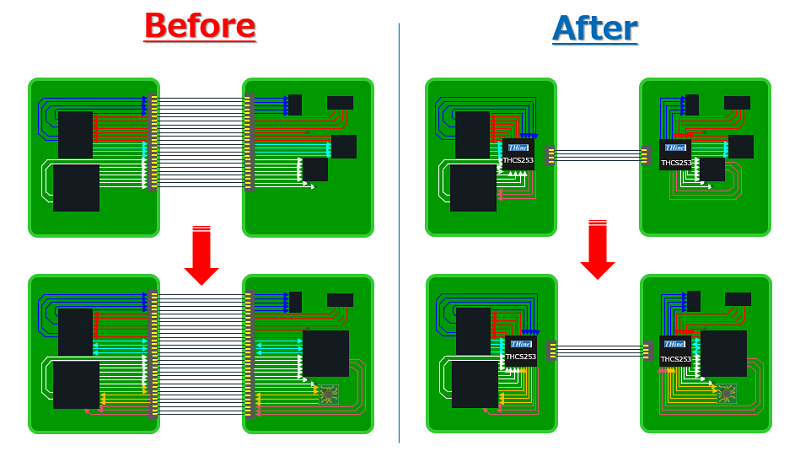
Fig. 4 Increased flexibility in hardware design
As mentioned above, the existing THCS251/THCS252 models also have a function that allows the number ratio of GPI and GPO to be set in four steps, which can be used to accommodate sudden design changes to some extent. However, the scope for customization is far more significant in our new models. Therefore, using our new models can significantly reduce the probability of redesigning hardware during design change compared to the previous models.
One might ask, "Was there no effective remedy that could prevent the need for hardware redesign?" Of course, this could be achieved using FPGAs. However, this brought a significant disadvantage ?increased design labor involved in designing the circuity inside the FPGA and the layout design of the printed circuit board. In addition, costs would increase. It would be difficult to decide to install FPGAs in the I/O section in advance simply due to the possibility of future change, such as the addition of functions, after starting the design in the first place.
However, the new models integrate the circuity for customization via I2C on a single chip, so unlike FPGAs, almost no additional design effort is required at the time of introduction. When other functions are added, they can be handled simply by rewriting the built-in registers, eliminating the need for any hardware redesign, such as signal transmission paths.
In Part 1 of this article, we described the changes made to the new THCS253/THCS254 models from the previous products, namely, I2C support in addition to GPIO, and introduce the advantages of this change, which is that the I/O section can be customized with a high degree of freedom (Fig. 5).
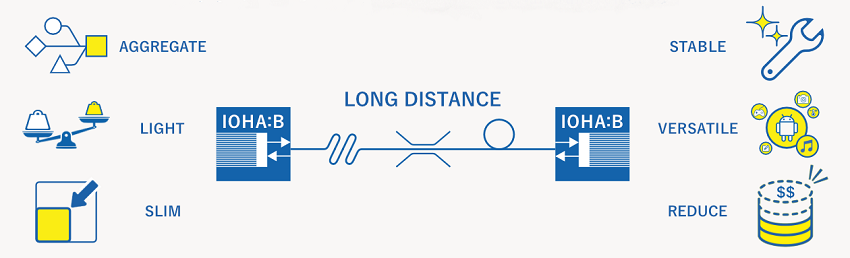
Fig. 5 Features of IOHA:B (THCS253/254)
In Part 2, in addition to explaining this change in more detail, another change, the introduction of synchronous/asynchronous mode, will be described.
End